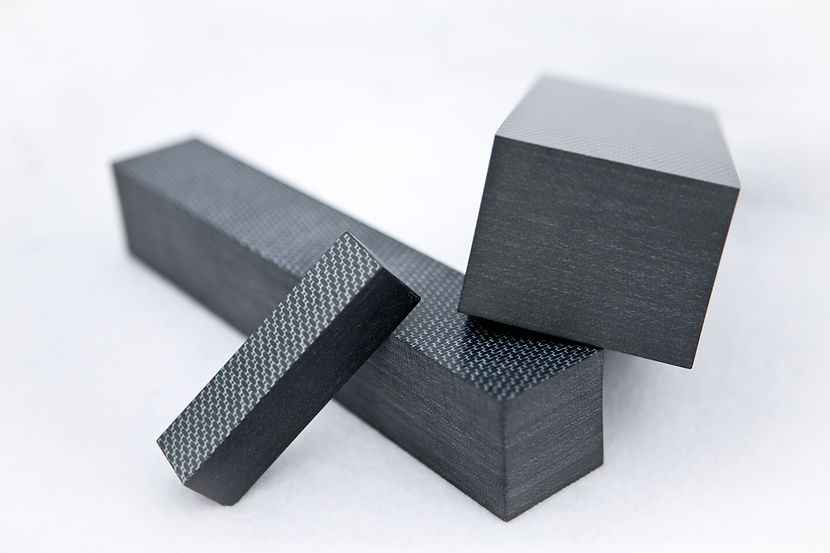
What is a Composite Material?
A Definitive Guide to;
- History
- Science
- Engineering
We all depend on composite materials in some aspect of our lives. Fiberglass was developed in the late 1940s and was the first modern composite. It's still the most common, making up about 65% of all the composites produced today. It's used for boat hulls, surfboards, sporting goods, swimming pool linings, building panels, and car bodies. You may well be using something made of fiberglass without knowing it.
Composite materials are formed by combining two or more materials that have quite different properties. The dissimilar materials work together to give the composite unique properties, but within the composite, you can easily tell the different materials apart – they do not dissolve or blend into each other.
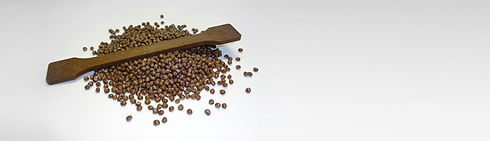
Brief History of Composites
In 3400 B.C the first composites were engineered by the Mesopotamians in Iraq. The ancient society glued wood strips on top of each other at different angles to create plywood. Following this, in around 2181 B.C the Egyptians started to make death masks out of linen or papyrus soaked in plaster. Later on, both of these societies started to reinforce their materials with straw to strengthen mud bricks, pottery, and boats.
​
In 1200 A.D, the Mongols began to engineer composite bows which were incredibly effective at the time. These were made out of wood, bamboo, bone, cattle tendons, horn, and silk bonded with pine resin.
​
Following the industrial revolution, synthetic resins started to take a solid form by using polymerization. In the 1900s this new-found knowledge about chemicals led to the creation of various plastics such as polyester, phenolic, and vinyl. Synthetics then started to be developed, Bakelite was created by the chemist Leo Baekeland. The fact that it did not conduct electricity and was heat resistant meant it could be widely used across many industries.
​
The 1930s was an incredibly important time for the advancement of composites. Glass fiber was introduced by Owens Corning who also started the first fiber-reinforced polymer (FRP) industry. The resins engineered during this era are still used to this day and, in 1936, unsaturated polyester resins were patented. Two years later, higher-performance resin systems became accessible.
​
The first carbon fiber was patented in 1961 and then became commercially available. Then, in the mid-1990s, composites were starting to become increasingly common in manufacturing and construction due to their relatively cheap cost compared to materials that had been used previously.
How to Make Composite Materials

Most composites are made up of just two materials. One material (the matrix or binder) surrounds and binds together a cluster of fibers or fragments of a much stronger material (the reinforcement). In the case of mud bricks, the two roles are taken by the mud and the straw; in concrete, by the cement and the aggregate; in a piece of wood, by the cellulose and the lignin. In fiberglass, the reinforcement is provided by fine threads or fibers of glass, often woven into a sort of cloth, and the matrix is a polymer.
The threads of glass in fiberglass are very strong under tension but they are also brittle and will snap if bent sharply. The matrix not only holds the fibers together but also protects them from damage by sharing any stress among them. The matrix is soft enough to be shaped with tools and can be softened by suitable solvents to allow repairs to be made. Any deformation of a sheet of fiberglass necessarily stretches some of the glass fibers, and they are able to resist this, so even a thin sheet is very strong. It is also quite light, which is an advantage in many applications.
By carefully choosing the reinforcement, the matrix, and the manufacturing process that brings them together, engineers can tailor the properties to meet specific requirements. They can, for example, make the composite sheet very strong in one direction by aligning the fibers that way, but weaker in another direction where strength is not so important. They can also select properties such as resistance to heat, chemicals, and weathering by choosing an appropriate matrix material.
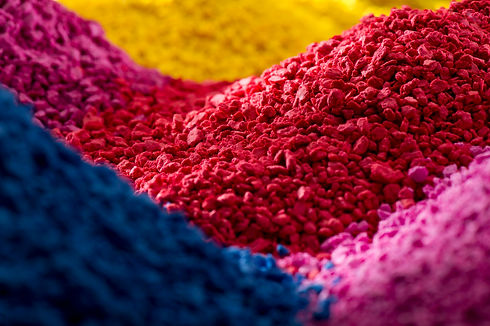
Selection of Matrix
For the matrix, many modern composites use thermosetting or thermoplastics polymers that hold the reinforcement together and help to determine the physical properties of the product.
​
Thermosetting plastics are liquid when prepared but harden and become rigid (ie, they cure) when they are heated. The setting process is irreversible, so that these materials do not become soft under elevated temperatures. These plastics also resist wear and attack by chemicals making them exceptionally durable, even when exposed to extreme environments.
​
Thermoplastics are hard at low temperatures but soften when they are heated. This class of polymers has some advantages, such as greater fracture toughness, the long shelf life of the raw material, the capacity for recycling, and a cleaner, safer workplace because organic solvents are not needed for the hardening process.
Selection of Reinforcements
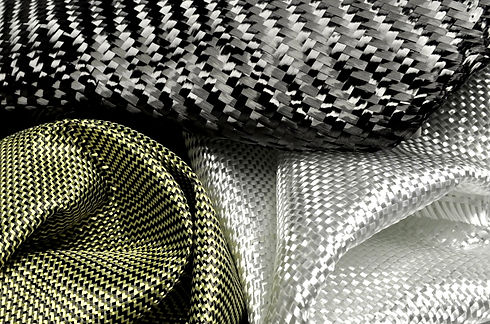
Although glass fibers are by far the most common reinforcement, many advanced composites now use fine fibers of pure carbon.
​
Glass fiber reinforced composites typically have a higher ultimate breaking point than a similarly shaped carbon fiber product. They are also cost-effective, powerful insulators, and very radiolucent. Glass fibers are manufactured by blending raw materials; silica (SiOâ‚‚) sand and additives designating the glass type, melting them in a furnace, at ~1400°C.
​
Carbon fiber composites are light and much stronger/stiffer than glass fibers but are also more expensive. Carbon fibers are used in aircraft structures and in high-performance sporting equipment like golf clubs, tennis rackets, and rowing boats, and are increasingly being used instead of metals to repair or replace damaged bones.
​
Polymers can also be used as the reinforcement material in composites. For example, Kevlar, originally developed to replace steel in radial tires but best known for its use in bullet-proof vests and helmets, is a polymer fiber that is immensely strong and adds toughness to a composite.

Manufacturing Processes
Making an object from a composite material usually involves some form of mold. The reinforcing material is first placed in the mold and then semi-liquid matrix material is sprayed or pumped in to form the object. Pressure may be applied to force out any air bubbles, and the mold is then heated to make the matrix set solid.
​
The molding process is often done by hand, but automatic processing by machines is becoming more common. One of these methods is called pultrusion (a term derived from the words 'pull' and 'extrusion'). This process is ideal for manufacturing products that are straight and have a constant cross-section, such as bridge beams.
The structure of many composites (such as those used in the wing and body panels of aircraft), consists of a honeycomb sandwiched between two skins of carbon-fiber reinforced composite material. These sandwich composites combine high strength, and particularly bending stiffness, with low weight.
Why Use Composites?

The greatest advantage of composite materials is strength and stiffness combined with lightness. By choosing an appropriate combination of reinforcement and matrix material, manufacturers can produce properties that exactly fit the requirements for a particular structure for a particular purpose.
​
Modern aviation would be much less efficient without composites. It is common now to find wing and tail sections, propellers, and rotor blades made from advanced composites, along with much of the internal structure and fittings. The airframes of some smaller aircraft are made entirely from composites, as are the wing, tail, and body panels of large commercial aircraft.
​
Composites are less likely than metals to break up completely under stress. The fibers in a composite act to block the widening of any small crack and to share the stress around in contrast to metals. In general, composite materials are exceptionally durable against heat, corrosion, chemicals, and the environment. Another advantage of composite materials is that they provide design flexibility. Composites can be molded into complex shapes – a great asset when producing something like a surfboard or a boat hull.
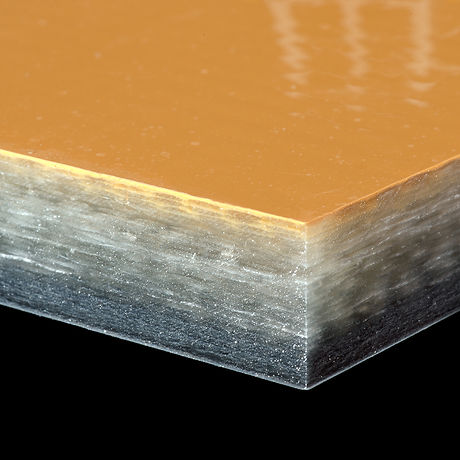
Industrial Composite Laminates
"Industrial laminates" is a special nomenclature for the panels made of thermoset polymer composites. Thanks to widespread and readily available utilization, especially in electrical systems, thermoset industrial laminates have their own standards which are published by NEMA (National Electrical Manufacturers Association).
Industrial laminates are thermoset resin impregnated reinforcing substrate materials that are cured under heat and pressure to form solid shapes having high mechanical and insulating properties. They are available in sheet, rod, tube and angle. Thermoset industrial laminates typically have a layered construction with at least two components:
-
The reinforcements such as woven glass cloth, random glass mat, glass filaments, woven canvas cotton fabric, paper, woven aramid fabric, random mat aramid, and others.
-
The thermoset resin binder that serves to adhere the layers of reinforcing substrates to each other to form a solid unit. Resin binders include epoxies, melamines, phenolics, polyesters, silicones and others.
In concert with member manufacturers, NEMA standards are set and "minimum values" published. The most commonly used NEMA thermoset laminate grades are described below.
Polyester Grades
NEMA grade Glass-Mat Reinforced Polyester -- GPO-1 (tan color), GPO-2 (red color) and GPO-3 (red color). These grades are composed of random mat (non-woven) fiberglass reinforcement held together by unsaturated polyester resin binder. Unsaturated polyesters are versatile resins which handle much like epoxies and are the best price-to-performance solution for most applications. Of course, the basic resins are chemically different. Polyesters, as compared with epoxies, show lower adhesion to most substrates, higher polymerization shrinkage, a greater tendency to crack during cure or in thermal shock and greater change of electrical properties in a humid environment. GPO-2 offers superior arc resistance over GPO-1 while GPO-3 offers both arc and track resistance. GPO-1 certifies to Mil-I-24768/4 GPO1; GPO-2 certifies to Mil-I-24768/5 GPO2 and GPO3 certifies to Mil-I-24768/6 GPO3.
​
Epoxy Grades
NEMA grades G10 and FR4 Glass-Cloth Reinforced Epoxy -- natural color is typically a yellowish to light green. The most versatile all-around laminate grades are continuous glass woven fabric impregnated with an epoxy resin binder. Epoxy resins are among the most versatile and widely used polymers in the electronics field, primarily because water absorption is virtually nil, rendering it an outstanding insulator. Beyond its electrical insulating properties, epoxy resins exhibit superior adhesive properties and great dimensional stability -- shrinkage is usually less than 1 percent. G10/FR4 has extremely high mechanical strength, good dielectric loss properties, and good electric strength properties, both wet and dry. The main difference between NEMA Grades G10 and FR4 is that FR4 is a fire retardant grade of G10. Therefore, FR4 can be safely substituted where G10 is called for, while G10 can never be substituted where FR4 is called for. G10 certifies to Mil-I-24768/2 GEE; FR4 certifies to Mil--24768/27 GEE-F.
NEMA grades G11 and FR5 Glass-Cloth Reinforced Epoxy -- natural color is typically yellow green to amber. This grade is similar to G10/FR4 with the addition of a higher operating temperature and some improved mechanical strength at elevated temperatures. The main difference between NEMA Grades G11 and FR5 is that FR5 is a fire retardant grade of G11. Therefore, FR5 can be safely substituted when G11 is called for, while G11 can never be substituted where FR5 is called for. G11 certifies to Mil-I-24768/3 GEB; FR5 certifies to Mil-I-24768/28 GEB-F.
Melamine Grades
NEMA grades G5 and G9 Glass-Cloth Reinforced Melamine -- natural color is typically a grayish brown. These grades are composed of a continuous glass woven cloth base impregnated with a melamine resin binder. Melamine resins, once cured, are the hardest, most rigid and abrasion resistant of the standard resins employed in the production of industrial laminates. However, prolonged exposure to high temperature can adversely affect its mechanical and electrical strength properties. Arc resistance, however, may remain unaffected despite excessive thermal exposure. Melamines are the hardest of laminates, exhibiting good dimensional stability and arc resistance. It's also caustic resistant. A key difference between NEMA Grades G5 and G9 are that G9 is more resistant to the elements of the environment. Thus, G9 can be safely substituted where G5 is called for. G5 certifies to Mil-I-24768/8 GMG; G9 certifies to Mil-I-24768/1 GME.
Silicone Grades
NEMA grade G7 Glass-Cloth Reinforced Silicone -- natural color is typically cream to white. Composed of a continuous glass woven clothe base impregnated with a silicone resin binder, this grade has excellent heat and arc resistance. Silicone thermosetting resins are among the best of all polymer materials in resistance to temperature. Hence, silicone is broadly used for high temperature electronic applications requiring low electrical losses. Silicone isn't as strong as epoxies and phenolics upon aging at lower temperatures but is stronger upon aging over 400° F. G7 has extremely good dielectric loss properties under dry conditions and good electrical properties under humid conditions, although the percentage of change is high. G7 certifies to Mil-I-24768/17 GSG.
​
Phenolic Paper Grades
NEMA grades X, XX and XXX Paper Reinforced Phenolic -- natural color is typically light tan to brown. These grades are composed of a paper base impregnated with a phenolic resin binder. Phenolics are the oldest, best-known general purpose thermoset resins. They are among the lowest in cost and easiest to process. Phenolics are quite adequate for a fair percentage of electrical applications. Generally speaking, they are not equivalent to epoxies in resistance to moisture, humidity, dimensional stability, shrinkage and retention of electrical properties in extreme environments. The paper reinforced phenolic has good electric strength properties with fair mechanical strength and are outstanding for use as template material and/or back-up material. A good rule of thumb in selecting a paper grade is to remember the more X's the better the electrical properties, while the fewer X's represent superior mechanical properties. Paper grades can be modified by adding plasticizers to make them more conductive to part punching resulting in a P suffix added to the X designation, i.e., XP, XXP, XXXP. Grade X certifies to Mil-I-24768/12 PBM; grade XX to Mil-I-24768/11 PBG; and grade XXX to Mil-I-24768/10 PBE.
Phenolic Cotton Grades
NEMA grades C, and CE Canvas Cotton-Cloth Reinforced Phenolic -- natural color is typically light tan to brown. C and CE grades are composed of a continuous cotton woven cloth impregnated with a phenolic resin binder. These grades contain a medium weave canvas and are known primarily for their mechanical properties. These grades are not recommended for primary electrical insulation. Grade C certifies to Mil-I-13768/16 FBM; grade CE certifies to Mil-I-24768/14 FBG.
NEMA grades L and LE Linen Cotton-Cloth Reinforced Phenolic -- natural color is typically light tan to brown. This grade is composed of a continuous cotton woven cloth impregnated with a phenolic resin binder. This grade contains a fine weave linen and, like the canvas phenolic, is known for its mechanical properties. The finer weave allows for machining more intricate details than canvas grade, such as gear teeth, etc. These grades are not recommended for primary electrical insulation, but grade LE exhibits superior moisture resistance to grades L, C and CE, and thus is an adequate insulator for a fair number of applications. Grade L certifies to Mil-I-24768/15 FBI; Grade LE certifies to Mil-I-24768/13 FBE.
Industrial laminates are used in many industries:
-
Electronics,
-
Electrical,
-
Machinery,
-
Automotive and Trucking,
-
Metal Finishing,
-
Aviation,
-
Chemical,
-
Home Appliance,
-
Textile.
Of these, the largest markets are electrical and electronics, thermoset industrial laminates provide strong reliable insulators for applications in:
-
Relays,
-
Bus Bars,
-
Washers,
-
Vanes,
-
Panels,
-
Coils,
-
Motors,
-
Gaskets,
-
Circuit Boards,
-
Switches,
-
Standoffs,
-
Arc Shields,
-
Test Boards,
-
Sockets,
-
Fuses,
-
Generators,
-
Transformers,
-
Condensers,
-
Terminal Strips.
